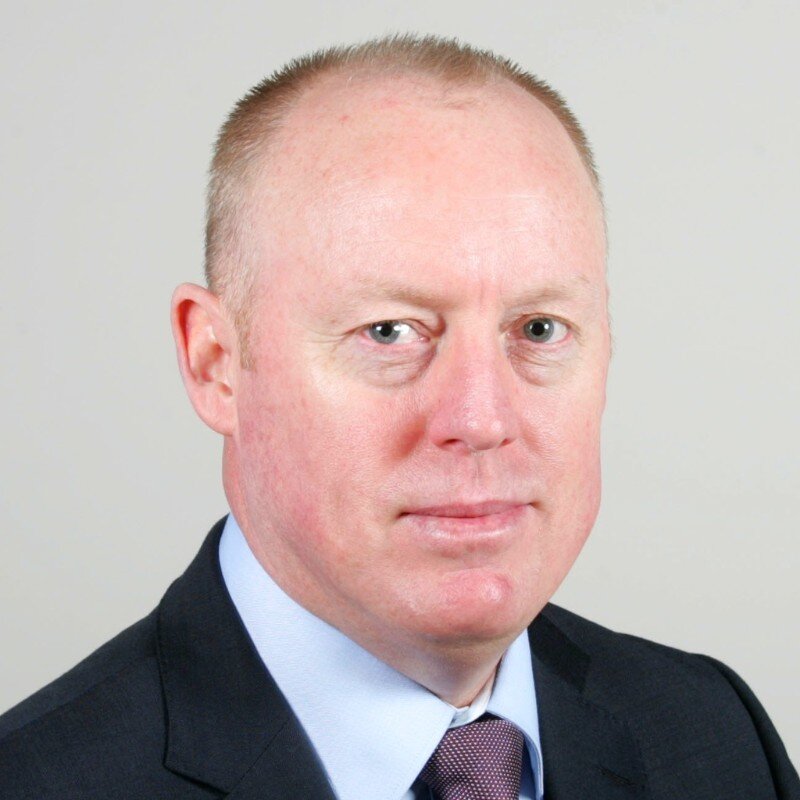
Paul Ceronio has 15 years of facilities management and operations experience in commercial/residential real estate. You can connect with him on LinkedIn.
------
I have managed many properties that have immaculate exteriors but are falling apart on the inside.
Over time, I began to realize that this was the status quo. Maintenance is an underestimated, neglected, contentious and misrepresented area of operations in real estate portfolios everywhere.
For me, the benefits of proper maintenance were always obvious. Not only does it save costs and thus have a direct benefit to asset value, but it also supports the reputation of the owner and helps avoid issues that cause tenants to move out.
But real estate is a complicated business and most portfolios don’t think this way.
In fact, when you mention maintenance in executive meetings, you usually see some combination of tuning out completely and conjuring negative memories: unplanned expense, inconvenience, extended time frames, finger pointing, and challenging contractor availability.
Even when I’ve been able to explain that the cost is real, immediate, and larger than perceived, the cure can sound worse than the disease.
Historically, I’ve advised making an organization-wide commitment to standardize a wide range of workflows and processes:
- Access
- Adverse weather management
- After-hour emergency procedures
- Alarms
- Archiving
- Automation technology
- Communication, progress, and completion
- Compliance
- Construction & maintenance works
- Environmental impact
- National disasters
- HVAC & plumbing
- Incidents
- Project management
- Security
Somewhat predictably, this list would be met with resistance: “There’s no bandwidth, no one will notice, we’ll pass the buck until we sell the property, it’s too costly, we’ve been operating this way for years – why change now?”
Fortunately, my advice is different now. Instead of trying to compile thousands of documents and spending hours putting together preventative maintenance and inspection schedules, my advice now is to embrace technology.
The ultimate goal is the same but now the medicine is easy to swallow.
Workflow Automation
According to Enertiv’s recent white paper, 30% of an operator’s time is spent on administrative work, another 16% is spent just walking around.
That sounds about right in my experience.
Any hours that can be transferred from non-value add work to “wrench time,” the fewer equipment breakdowns and expensive repair calls.
There are plenty of opportunities for automation. Many properties are doing things the same way as when I first started my career. Each day, time is spent prepping for the day’s work: printing out maintenance schedules, coordinating with property managers, and prioritizing work orders.
All of that can now be done instantly on mobile apps.
Sensors can take workflow automation to the next level and pay for themselves twice over in the first year.
For example, many properties think they’re already using technology by letting tenants submit work orders.
I think that’s backwards. When it comes to any system of consequence, by the time a tenant is aware of the problem, things are already in very bad shape.
Why not have the building itself generates work orders automatically with sensor data, backed up by analytics to pinpoint the root cause of the problem. This same sensor data can bid out and order necessary parts, monitor for a resolution to the problem, fill out the details in the work order and archive it in a digital form.
This setup doesn’t even require a building automation system, these sensors can be installed in any building.
Building Automation Back Up
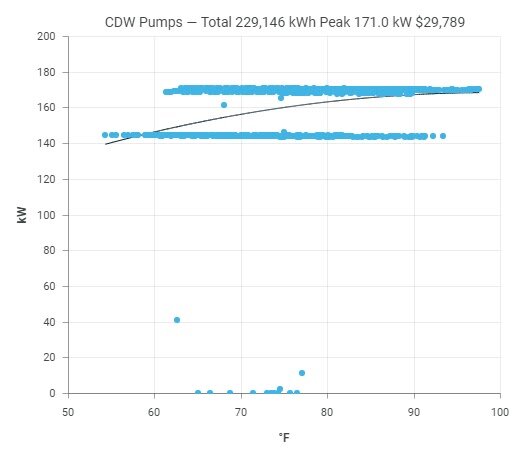
Speaking of building automation systems, one of the most beneficial aspects of new technologies is serving as a redundancy to the building automation systems in place.
When an engineer programs an automation system, they expect their instructions to be carried out. Discovering that a controller is malfunctioning, and subsequently that none of your instructions have been carried out, is very difficult to diagnose.
These systems can cost upwards of a million dollars, we can be forgiven to expect them to just work. How long would it take you to figure out that 10% of your emails never actually get sent even when it says they have?
With sensor data, these common issues are identified immediately. Proactive maintenance doesn’t just apply to equipment, it also applies to the systems that control equipment. If you want to see the ROI you’ve expected on automation, make sure it’s backed up.
Business Continuity Plan
The lesson from COVID-19 isn’t that we only need to be better prepared for pandemics, it’s that things that can go wrong without a moment’s notice in real estate management.
There can be a failure of IT systems, power failure, water supply shortages, restricted access due to emergencies in the area, public transport failure, terrorist attacks, social upheaval, etc.
Technology helps ensure you have a fail proof business continuity plan by infusing your operations with resilience and flexibility. Too much information about how to operate buildings is held precariously in the minds of engineers.
There’s no time like the present to put that knowledge in a computer:
- List of critical equipment and parts
- Software and systems used and how they’re integrated
- Service agreements
- Plans in case of an interruption in gas, electricity, water, sewage, trash removal, etc.
Environmental Impact:
Commercial real estate has never been so focused on the environmental impacts of their operations. Towards this goal is another example of how maintenance is overlooked.
The following summarizes studies of the potential energy savings from good maintenance on chiller components alone:
- Tube cleanliness: 10-35% savings
- Ensuring proper condenser flow: 3% savings
- Ensuring proper refrigerant levels: up to 20% savings
- Cleaning refrigerant of oil contamination: 2% savings for every 1% of oil found in the refrigerant (it’s not uncommon to find 10% oil in older chillers)
- Eliminating leaks in compressors: 6-14% savings
- Ensuring functioning economizer: 14-40% savings
- Ensuring proper airflow: 10% savings
- Eliminating thermostat control problems: up to 40% savings
- Eliminating sensor problems: up to 40% savings
Environmental, social and governance impact must be part of your business policy and strategy. Proper maintenance should be part of your ESG strategy. Technology should be at the foundation of your maintenance strategy.
Final Word of Advice
There are clear financial benefits to leveraging technology to implement proper maintenance practices. The value of proactive maintenance includes:
- Prevention of equipment downtime
- Prevention of inconvenience and increases confidence in your residents, staff, client, etc.
- Prevention of future, unexpected and expensive equipment breakdowns
- Saving on insurance claims and prevents increased premiums
- Assisting with preventing and reducing the risk of injuries or fatalities to staff, visitors, contractors, tenants, etc.
Beyond that, it makes the lives of people like me easier and happier.
Would you like an average or just manageable site where staff are demotivated, the place verge of collapse and you hold your breath when buyers do due diligence?
If not, then invest and be proud of a professionally managed, safe, reliable, and attractive real estate site. Staff and residents will also be proud to be associated with the site and investor eager to invest.
Want to see the type of technology Paul is talking about? Watch a demo video of the Enertiv Platform today to see how it works.