Introduction
A few weeks ago, we announced a milestone of 10 billion hours of building performance data captured. To make that more tangible, we outlined 10 practical examples of how our clients are using this data and how this data helps to identify reasons for budget variance.
But there’s a critical ingredient that deserves more attention.
That is, data that can’t be converted into “hours.” The digitization of the physical documents, materials, processes, and assets that come with owning and operating commercial real estate.
More specifically, moving equipment information like ages and models into the cloud, digitizing files such as mechanical diagrams and maintenance manuals, and shifting processes off clipboards and spreadsheets and into apps and software.
While not as sexy as real-time sensor data, this backend digitization is invaluable.
You see, here at Enertiv, we figured out the hard part first. Developing and integrating new sensors, building out an international network of installers, creating the systems and infrastructure necessary to connect and maintain thousands of devices around the world is all very difficult.
Comparatively, backend digitization has been straightforward. Just as importantly, it has made the difficult part much easier. Now, in the process of doing daily workflows, operators are creating a detailed map of their building’s infrastructure as a byproduct.
So, while the full range of capabilities of a smart building are exciting, it’s important to understand that picking the low hanging fruit produces real and immediate value in the near term.
Asset Tagging
Before connecting to the BMS or installing sensors to track equipment performance, a full-scale inventory of every piece of equipment can be created with photographs and asset tags.
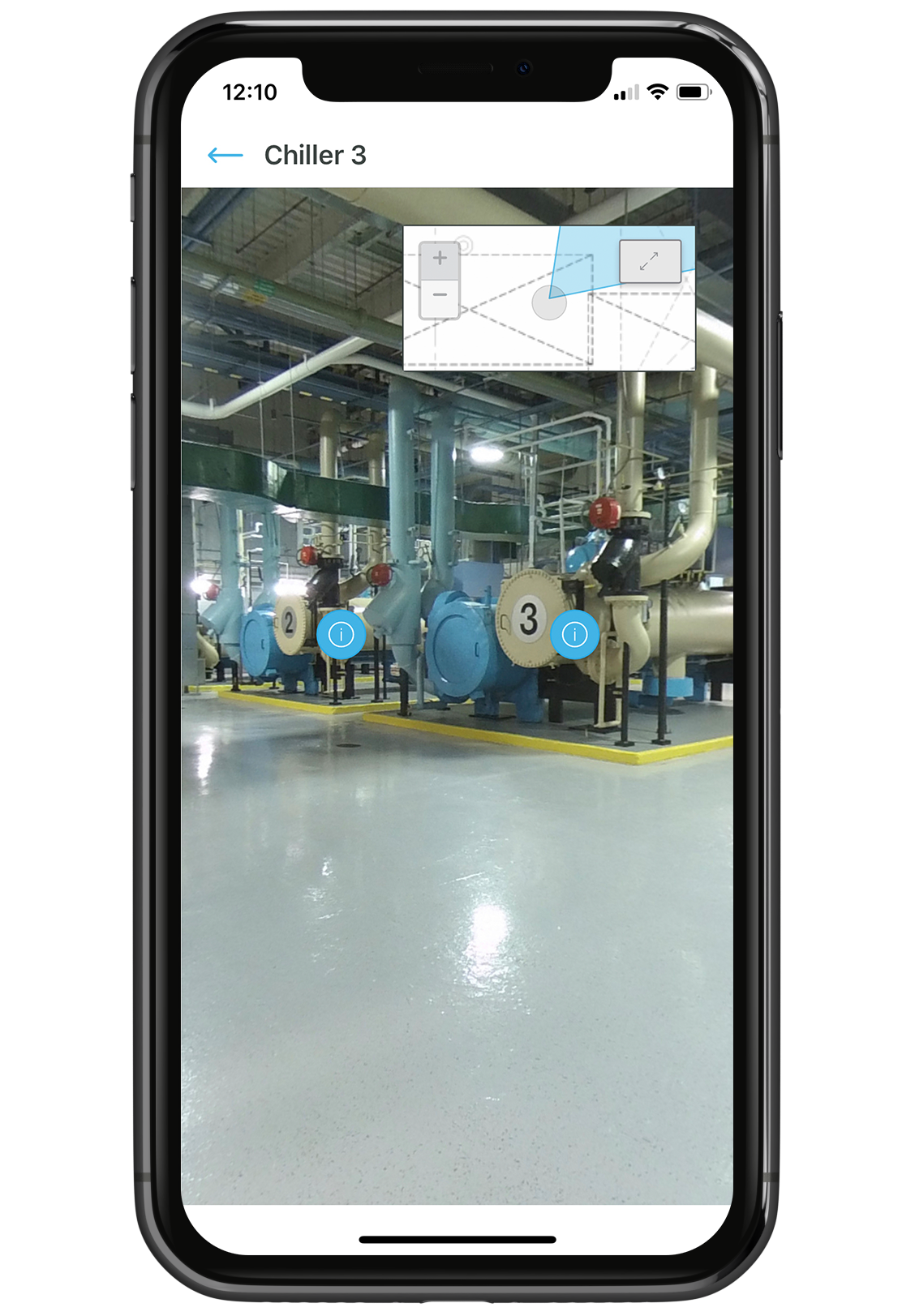
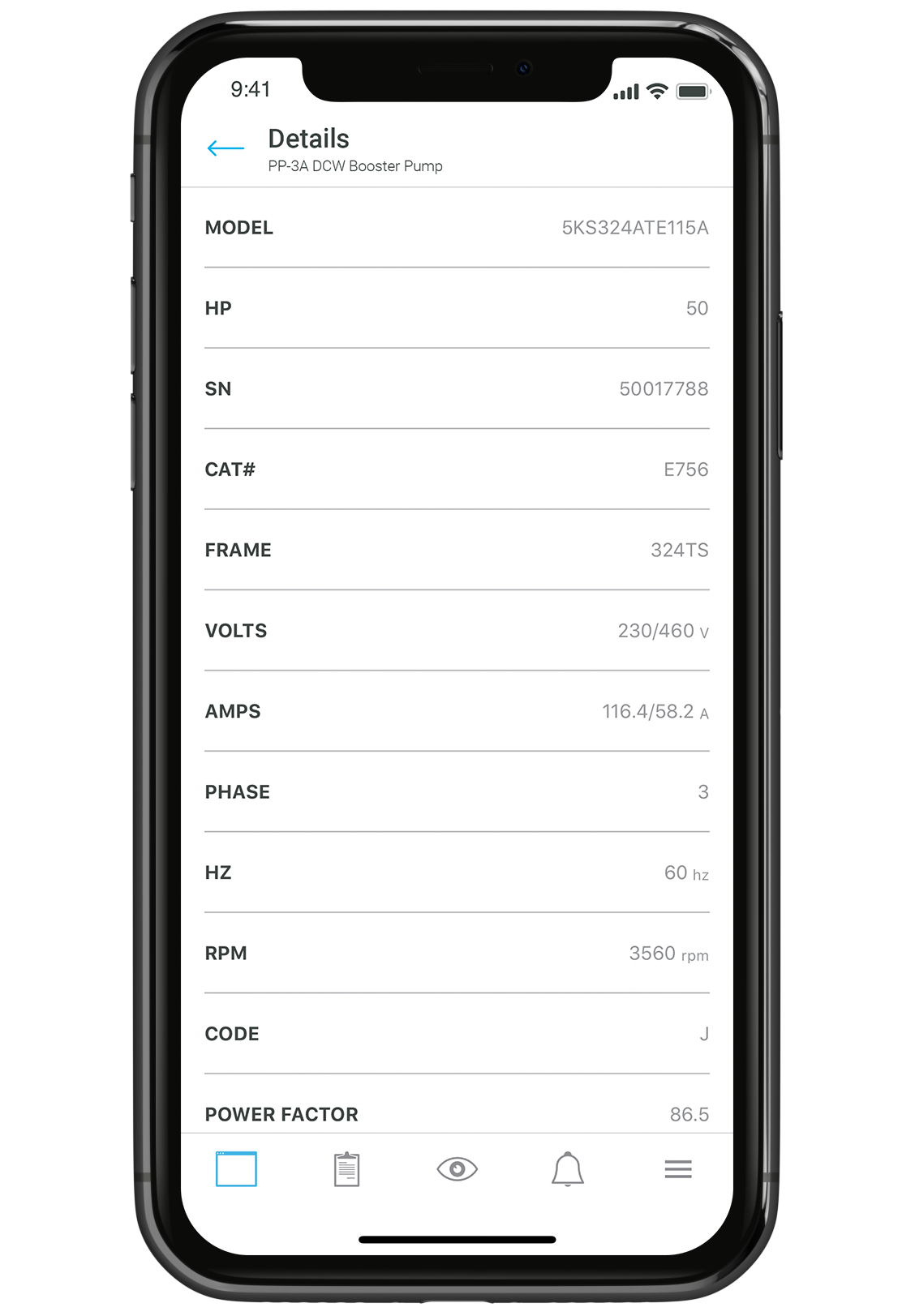
Instead of all the issues that come with spreadsheets, there is now a living, breathing inventory of every piece of equipment across the portfolio, complete with equipment nameplate information, age, and replacement value.
Each piece of equipment can be further broken down into individual components and the parts necessary for repairs. With this in place, the introduction of real-time data can be very powerful.
Imagine this: an equipment breaks down and because of this initial digitization, the software knows how it broke down and creates bids for the needed parts, all the operator needs to do is press one button to order.
Rounds and Preventative Maintenance
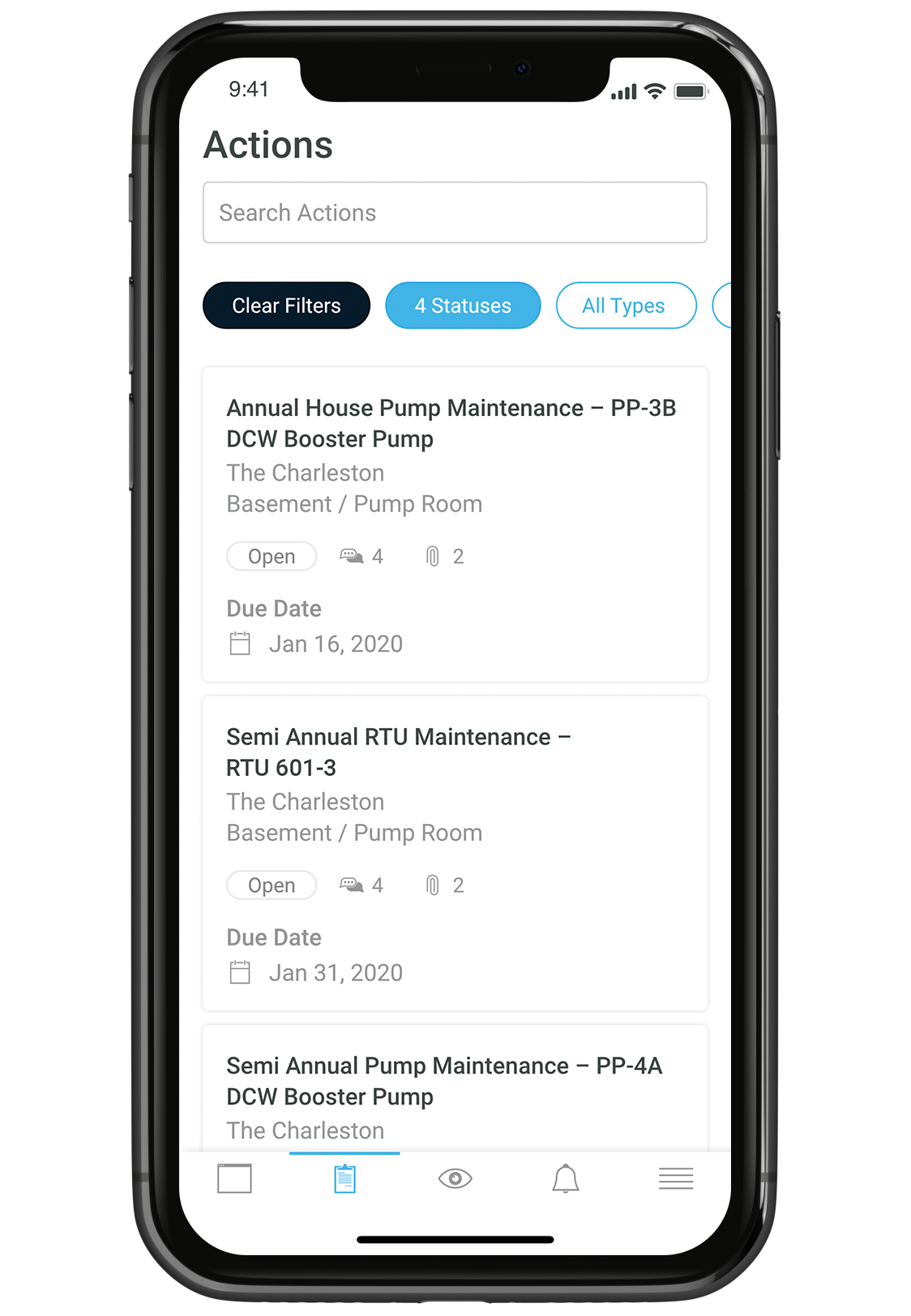
Real-time equipment data can unlock several powerful functions, including fault detection, maintenance schedules based on runtime hours instead of calendars, and optimized schedules and set points.
But prior to these more advanced capabilities, a lot of value can be derived simply by moving rounds and preventative maintenance from clipboards and spreadsheets onto mobile apps and software.
In fact, when maintenance activities are coupled with asset tagging mentioned above, a lot of transparency can be created very quickly.
For example, many landlords use multiple real estate services companies to manage their properties in different markets. Imagine making data-driven decisions about which companies are maintaining the assets most diligently.
Likewise, for triple net leased assets, this can provide insight into whether tenants are in compliance with their maintenance responsibilities. If not, the data is available when a repair or replacement arises, a lease comes up for re-negotiation, or a tenant is ready to move out.
Finally, this digitization can standardize property condition assessments. Too often, asset managers have to make decisions about capital expenditures with limited information and potentially diverging opinions between engineers on the condition of equipment. While real-time sensor data can effectively pinpoint degradation over time, digitizing property condition assessments can also help smooth out human variance and improve decision making.
Meter Reads
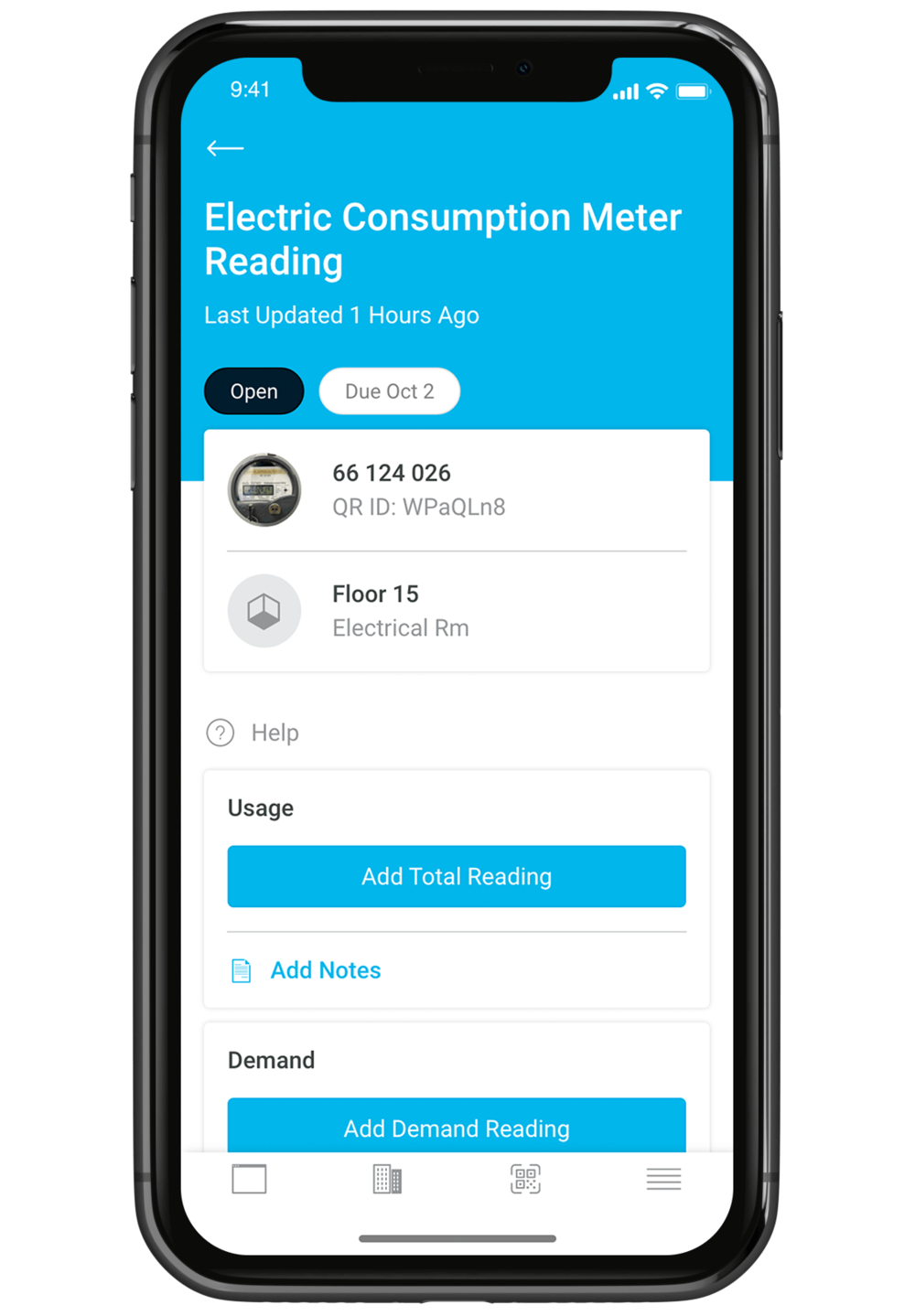
It’s entirely possible to upgrade a submetering infrastructure to digital, remotely-readable meters. With this setup, the tenant billing process, from data collection to bill generation, can be fully automated. But upgrading a metering infrastructure is a big capital expense that some might not have the budget for.
In these cases, the current process can be improved without any capital expense while simultaneously making the upgrade to digital meters easier down the road.
That digitization is very similar to rounds, except instead of scanning asset tags and performing inspections and maintenance actions, operators scan tags placed on the meters and enter the consumption readings (as well as a picture for record keeping).
Instead of having to be transcribed from clipboards into spreadsheets and then into bills, the meter reading is uploaded directly into the cloud, where software can automatically archive all of the information and generate bills.
One of the side benefits of this is that in the process of taking meter readings, the infrastructure itself is getting documented. This may not seem like much, but it’s critical for creating a plan to upgrade the infrastructure.
Documentation
99% of the time, nobody needs mechanical plans, riser diagrams, electrical schedules, equipment brochures, spec sheets and countless other documents. For this reason, they are generally stored haphazardly in filing cabinets, taped to equipment, or lost.
But when the moment comes that one of these become necessary, time is usually of the essence.
For example, sophisticated tenants often request documentation and equipment information before signing a net lease. Spending weeks to collect this data can risk losing a leasing deal.
Likewise, large real estate portfolios have hundreds or thousands of individual service agreements. These are safely in effect for years without anyone having to worry about them. But once they start expiring, services are usually needed right away and it’s nearly impossible to get organized.
While sensor data can provide alerts about how equipment operations, alerts can also be setup based on when service agreement are set to expire so no one has to remember to stay on top of them and work can be handled in a more organized fashion.
Conclusion
The point is, while sensors, smart buildings, digital twins and all the other buzzwords floating around are worth pursuing in the long run, there is a lot of low hanging fruit to pick today.
Not only does basic digitization provide immediate value (that can be quickly scaled), it maps the current infrastructure in a way that is extremely helpful for layering more sophisticated monitoring in the future.
In fact, this type of digitization is a prerequisite to producing insights at scale because billions of hours of data are simply too much to look through manually. Being able to categorize and segment sensor data is critical. If you want to learn more about that, here’s a great video one of our data scientists made:
And If you’re looking to digitize your real estate portfolio, we’d be happy to provide a demo video of the platform.