Introduction
Last week we explored the value of digitization and asset tagging when it comes to capital planning.
Getting out of spreadsheets, PDFs and email archives would be a giant leap forward for most real estate portfolios. It would translate to saved time, a smoother budgeting season, and better cohesion between different departments.
But the goal is to fix the capital planning process. We can’t stop at democratizing information, we have to focus on improving decision making.
There are always going to be competing factors when it comes to capital planning: the cash flow of the property, the bandwidth of the on-site teams and asset manager, the fund’s target hold period, and more.
Those are not going away. But all of these should be weighed relative to the most important criteria: the real-world condition of the equipment.
Unfortunately, the true equipment condition is unknown for most discussions. Perhaps there’s a property condition assessment from a while back, or maybe some anecdotal evidence from an on-site operator, but nothing systematic.
Without this, portfolios are spending money on equipment and infrastructure that could’ve been replaced at a later date. At the same time, they are deferring investments that end up costing more in ongoing repairs, operator time, and tenant attrition.
That’s where integrating maintenance data comes into play.
What’s the condition?
A decent sized commercial real estate portfolio will own tens of thousands of individual pieces of equipment. It’s seemingly impossible to stay on top of the condition of each one ahead of budgeting season.
And so, asset managers are forced to fall back on the latest property condition assessment (PCA).
While very thorough at the time of completion, a PCA is just a snapshot in time.
They are too expensive to have done on a regular basis, and so the observations of one day tend to serve as the basis for decision making years later.
Ironically, there’s a ton of valuable information being collected daily, weekly, and monthly that is being ignored. Operators are performing rounds and inspections based on a predefined checklist, third party maintenance vendors are providing service reports, replacement parts are being ordered and work orders are being completed.
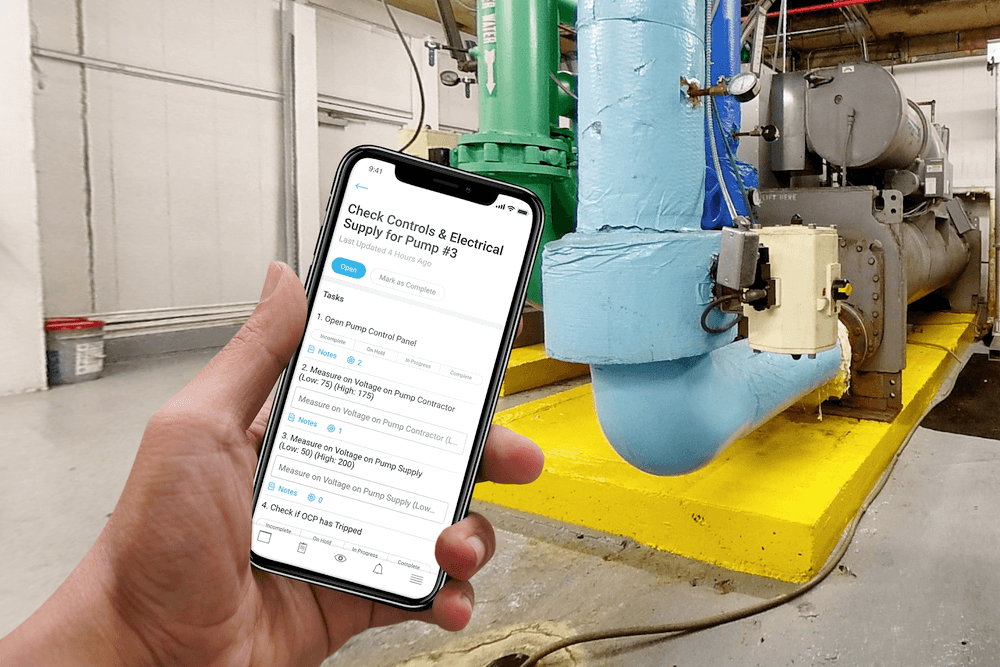
The problem is that this data ends up on a piece of paper shoved into a filing cabinet, emails, or best case, lives in a software that is disconnected from the capital planning process.
Decision making can be greatly improved if we simply utilize this data that is being created every day.

If a piece of equipment is up for a replacement according to the original PCA, but has passed every inspection with flying colors and has been consistently maintained, we should know that and look to defer that expenditure.
On the other hand, a piece of equipment that looked fine during the PCA, but that has consistently failed inspections might be moved up based on the understanding that it is ultimately costing more money to maintain and fix it than it would be to replace it.
Doing what humans can’t
Integrating routine inspections and work order data into capital planning is a great first step to better decision making.
But why stop there. It is affordable to monitor equipment continuously by integrating with building management systems or by deploying sensors. Doing so comes with a host of benefits including energy savings, real-time alerts, and predictive maintenance insights.
And there’s a particular benefit relevant to improving capital planning decisions: calculating runtime hours.
Runtime hours are like the odometer for equipment.
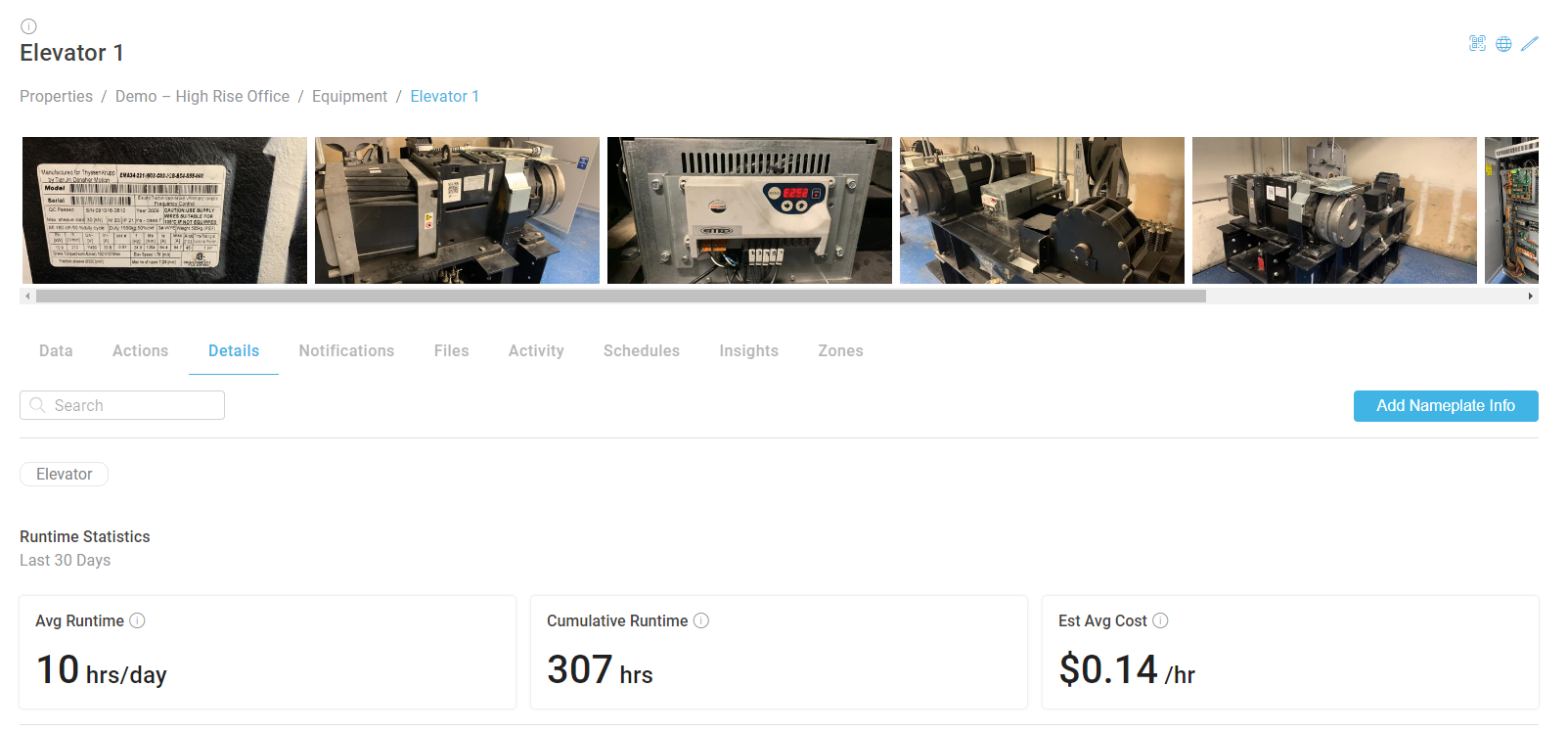
Making capital decisions without runtime hours is like buying a new car based on how many years you’ve owned it, regardless of how many miles you have driven it.
Sure, there are estimates and averages out there, but if there’s anything commercial real estate knows, it’s that you can’t apply broad averages to the particular situation of an asset.
Similar to the examples above, you may decide to defer replacing that boiler because it hasn’t been run as much as expected over its lifetime.
The same real-time data could add more dimensions as well. For example, how frequent and severe have the faults detected for this boiler been? Have they been resolved in a timely manner?
Conclusion
The status quo involves capital plans living in spreadsheets, relevant documents in email archives, messy forecasts, best guesses, and long meetings.
Now imagine: equipment inventories are digitized, capital plans live in software, documents are centralized and easily accessible, and decisions are based on a very good sense of the current, real-world conditions of the asset.
As different as those two scenarios are, the gap is not that wide. Unlike other difficult operational problems, the data does exist, it’s just a matter of consolidation.
And the incentive is there. Equipment and infrastructure projects cost huge amounts of capital and decisions made today will affect the property’s cash flows for decades.
In fact, unexpected equipment replacements are one of, if not the single largest risk to owning or purchasing an asset.
In the long term, sellers who can show that the capital plan they’ve been following has been based on significantly better data than anything the industry has seen before may be able to increase purchase price by demonstrably reducing the risk premium for the buyer.
Want to learn more? Watch Enertiv Office Hours
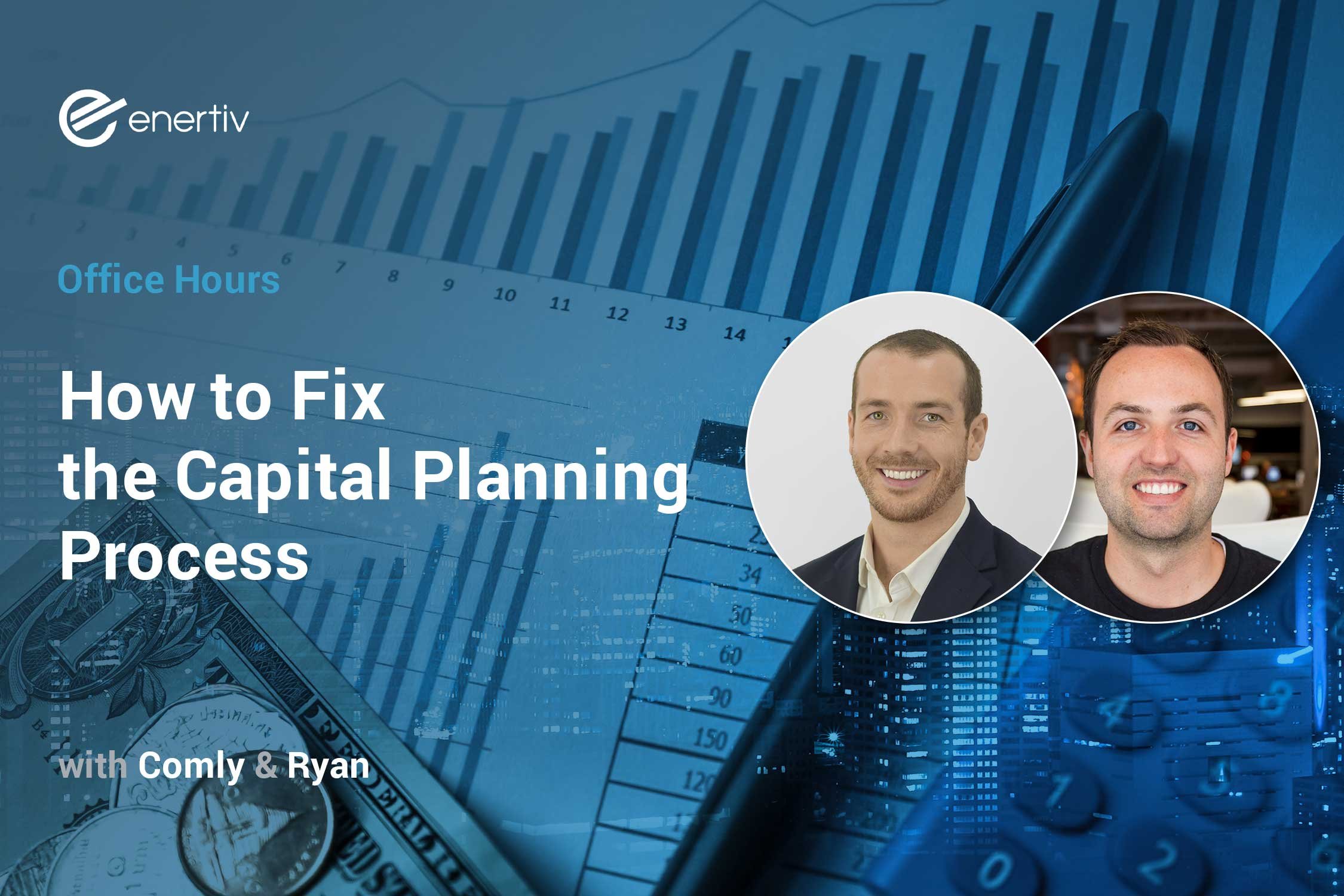